Are You Prepared for a Water Main Break?
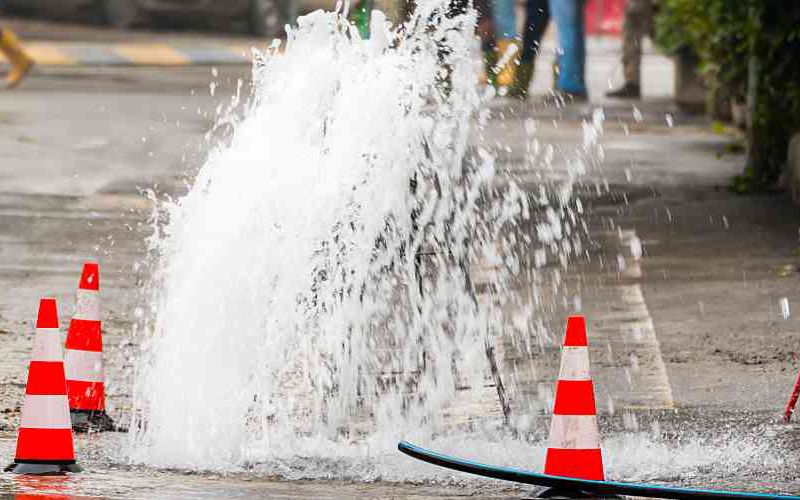
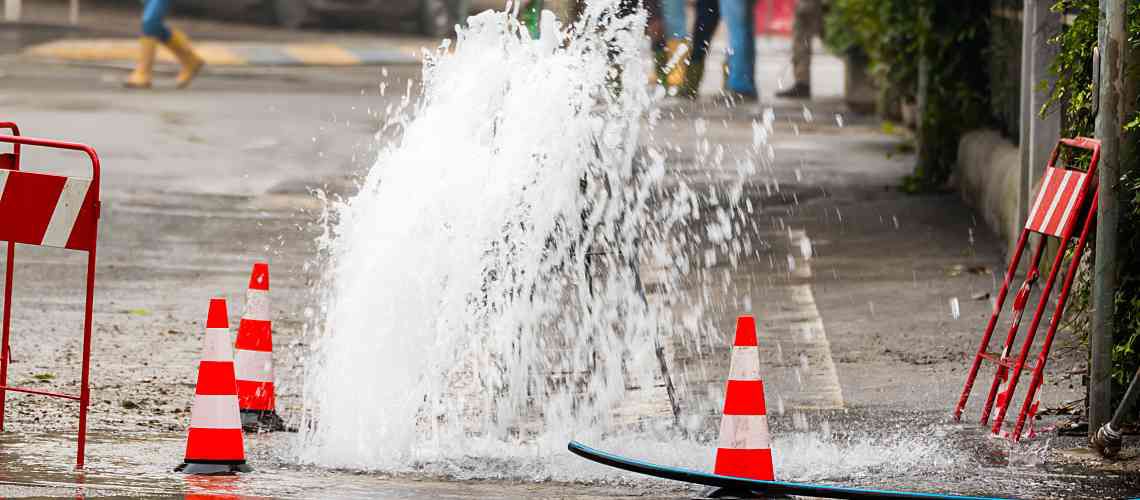
Water main break rates jumped 27% from 2012 to 2018, according to comprehensive survey data from Utah State University, with small utilities experiencing more than double the incidents of larger ones. Winter is the peak time for pipes to burst, as they expand and crack under the stress of freezing temperatures. Add in aging water infrastructure and it's a recipe for disaster.
However, breaks can happen at any time. The American Society of Civil Engineers reports that in the United States, an estimated 240,000 water main breaks occur every year. As a water utilities lab manager, you'll need to be prepared to both handle main breaks and the spike in activity that follows them.
Here are the testing requirements you'll need to know, as well as some strategies to minimize the impact of water main breaks on your customers and budget.
Risks and Requirements in a Water Main Break
A pressing concern with water main breaks is potential fecal contamination. This can occur when unpressurized pipes allow surrounding soil and groundwater to infiltrate water supplies. State regulations determine the steps utilities must take after a water main break. These usually follow similar best practices, including:
- Performing water testing for total coliforms at multiple locations downstream of the repair, with the number determined by the population affected by the break.
- Testing two sets of samples 24 hours apart before lifting boil orders and resuming normal service.
- Notifying state environmental authorities when a sample tests positive for E. coli.
- Testing the original sampling locations for residual chlorine after disinfection.
You can find more information on sampling best practices in the American Water Works Association's standard on Disinfecting Water Mains. You may also refer to state-specific requirements, such as the New Jersey Department of Environmental Protection's Water Main Break Guidance Manual.
Ways to Prepare for Water Main Breaks
In addition to following these recommendations, there are a few provisions you can make to reduce service interruptions and costs associated with water main breaks.
Have Testing Supplies at the Ready
If your lab tests samples in-house, you'll need a balanced inventory. That means having enough supplies on hand to meet demands, without overstocking to the point where products expire unused. This balance will look different for each lab, depending on the size of the utility and the number of customers it services.
One strategy for striking this balance is looking at the number of samples you've processed in previous winters. Labs that process external samples can also benefit from this practice, as it may help them better prepare for surges in requests.
Also, consider how the tests you carry will affect staffing. Some E. coli tests offer results in 18 hours, while others take 24 hours. With 18-hour tests, any samples that come in Friday can be read early Saturday morning. In the same scenario, 24-hour tests will require someone to come in Saturday evening to read the results.
Be Ready to Ship
It's a simple reality: Many smaller water utilities cannot process all their samples on-site. If this situation applies to you, it's critical to have sampling bottles and shipping supplies ready at all times. This way, samples can be swiftly sent out for testing and service can be quickly restored to customers.
It's also smart to proactively strengthen contracts with labs you plan to ship samples to. That way, when you need a large number of samples tested, you don't have to worry about negotiations because you already have established procedures in place. The last thing you want is to be searching for support labs while dealing with a water main break.
Review Lab Procedures
Whether you do all your testing in-house or rely on other labs for supplemental testing, it makes sense to review your processes and procedures before a crisis occurs. In doing so, you'll want to focus on areas like:
- Testing procedures: In addition to managing inventory levels, you'll want to evaluate whether your protocols are effective and efficient at handling a large influx of samples.
- Emergency response plans: Updating your response plan ensures you aren't caught off guard with a surge of samples, and that everyone knows their role in handling an incident.
- Employee training processes: Checking that employees are up to date on training requirements, specifically surrounding performing E. coli tests, helps ensure you have the appropriate staff resources in place to efficiently process samples.
Winter can cause big headaches for water utility labs caught unprepared for main breaks. To tackle this influx in critical samples, you'll want to strategically stock up on testing supplies, strengthen agreements with external labs, and review internal processes. Taking these measures will help ensure your team stays ahead of the curve, keeping the impact on your customers and operational budget minimal.