Avoid Errors in Your Water Lab With These 6 Prevention Strategies
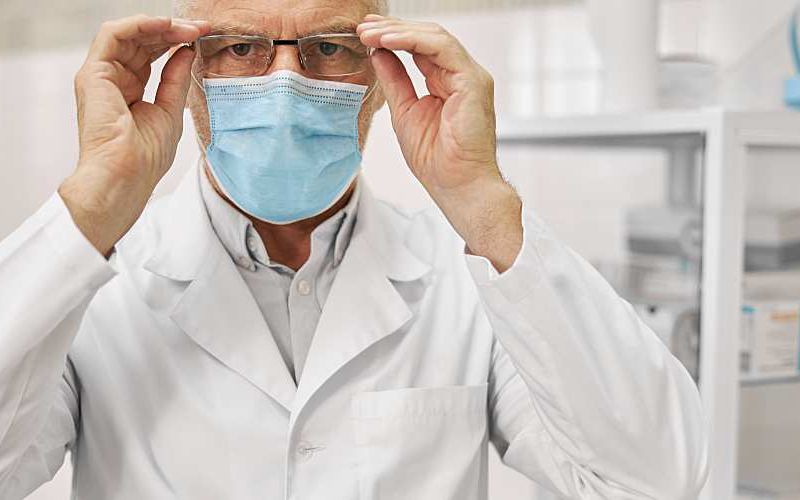
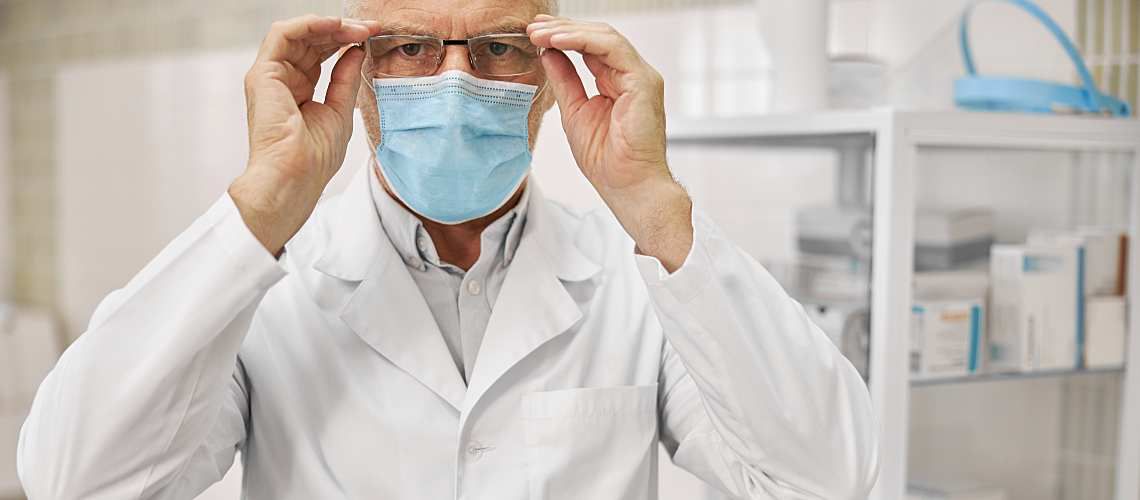
It's 10 a.m. on a Monday when you notice smoke coming from a thermoreactor used for testing water samples. Not keeping up with instrument maintenance now means delaying testing for weeks while waiting for new equipment — all because someone forgot to put in a service call.
This scenario is one of many lab errors that managers must work to prevent. Other mistakes range from management missteps, like making bad hires and ineffective marketing, to operational errors, like not using controls appropriately.
With all that in mind, consider adopting these prevention strategies to help avoid common mistakes and ensure better efficiency in your lab overall.
1. Implement a Preventive Maintenance Program
Equipment maintenance mistakes are some of the most expensive and time-consuming errors that labs face. Part of the problem is that, in an effort to cut costs, water labs may only deal with equipment once it breaks down.
A better method is to invest in preventing breakdowns altogether. Preventive maintenance involves performing regular cleaning, repairs, and part replacements to minimize downtime.
Depending on the instrument, you might perform maintenance on a specific calendar date or after a certain amount of runtime. Service contracts can also help, but you should carefully evaluate the cost of service calls, whether parts are covered, and whether you can afford to replace the instrument.
2. Develop a Marketing Plan
If you're worried about missing out on new business, a good place to start is with a marketing plan. Your marketing plan should do the following:
- Assess strengths, weaknesses, opportunities, and threats (SWOT analysis), with an eye toward uncovering new opportunities or potential customers.
- Include different personas or ideal customer profiles (e.g., environmental, municipal, etc.) to understand their top challenges and how they learn about services like yours.
- Establish specific goals that you want to achieve.
- Outline what makes your lab unique and why customers should work with you.
- Determine which channels you'll use to achieve your goals, such as your website or direct outreach.
- Describe the tactics you'll use to achieve your goals — for example, by attending virtual events or by hosting educational webinars.
3. Listen to Your Customers
One way to grow your business and prevent a lag in new clients is to talk to your best customers to determine how to better serve them and how to get more customers like them. Ask your best clients these questions:
- Why did you choose to work with us? The answer can help you understand what to focus on in your marketing materials.
- What would make your life easier? Your customer's response can provide new ideas for how to differentiate your services.
- What are your biggest problems? The answer to this question can also spark ideas on how to make yourself indispensable to clients.
Empathetic listening is also critical to managing complaints. Rather than reacting defensively, acknowledge the error and let the customer vent. You should also ask how to make it right, then do your best to make it happen.
4. Create a Rock Star Team
When you have a critical staffing need, it's easy to let urgency get in the way of the long-term view. Unfortunately, the wrong hire will cost you big if you have to replace that person within six months.
How can you strategically build a team of rock stars?
- Ask detailed questions. Give people testing scenarios and ask them how they would handle the situation. Any question that requires the person to walk through a series of steps will reveal their true experience level, so you don't just have to rely on the resume.
- Create room to move up. Outside of higher pay, providing development opportunities is one of the top ways to improve employee retention. In fact, according to CNBC, 94% of employees would stay with their company if it invested in helping them grow professionally.
- Give people feedback. Employees are more engaged when they know how they are doing, get praised for good work, and recognize how they can improve. You should do this regularly in addition to annual performance reviews.
- Solicit suggestions. Ask employees what would make their jobs easier or more enjoyable. Then, make sure to implement whatever suggestions you can (otherwise people won't keep sharing ideas).
You also want to make sure you tackle issues with challenging employees head-on, given that problem employees can make other valuable team members want to leave.
5. Make Safety a Process — Not an Event
Labs are risky places to work. Fire, inhalation of fumes, tripping on cords — all of these and more can hurt employees and lead to legal and regulatory problems. Lax safety may also hurt morale and increase turnover.
Rather than making safety training a one-and-done event, it should be an ongoing process that involves:
- Training people in behavior-based safety approaches so everyone feels comfortable speaking up when they see safety issues.
- Conducting daily walk-throughs where you observe and provide respectful feedback on safety conditions.
- Analyzing near-misses to understand where future issues are likely to happen.
6. Review Use of Standards and Controls
Inconsistent use of standards and controls is a widespread problem that affects the accuracy of results for many labs. Get it wrong, and you could face an increase in customer complaints as well as weeks (or more) of invalid data.
Standards demonstrate that an assay delivers the expected results, and they are used to calibrate an instrument. Controls should be used to ensure they are operating within an established range of acceptable values. Although you likely understand the distinction, it's worth reviewing with employees to make sure they're running a control with every analysis to assess for drift. Solid technicians may already be well aware of this, but it's definitely something to look for with newbies.
Lab management involves many moving pieces, and mistakes will happen. Focusing on the preventive strategies discussed here can help you get ahead of problems — and turn the ones that do happen into improvement opportunities.